Over the last 20 years, technology has not only improved but significantly impacted the manufacturing sector with regard to the production of parts and prototypes. The inceptions of computer systems have improved the accuracy and precision of the manufacturing process.
In the modern production sector; rapid tooling, CNC machining, and prototype molds are the basic rule of thumb is you want to stay productive and competitive. Reducing overall cost is what most clients are looking for nowadays thus manufacturers have to keep up with the changing trends in the production process.
Despite all the advantages of an automated production procedure, manufacturers still face their fair share of challenges and flaws. For this article, we are going to briefly highlight tips on how you can counter rapid tooling design flaws.
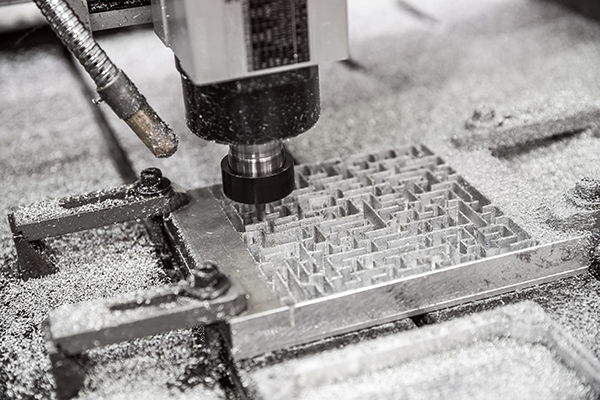
CNC Milling*
CNC milling is from eaglegroupmanufacturers.com
Problems/issues with troubleshooting
Troubleshooting is part and parcel of the manufacturing process, let’s just be honest; this phase is the most stressful and time-consuming. A lot of test runs have to be carried out to point-out flaws and performance issues so that it can be rectified.
Troubleshooting is the only part of the production process that cannot be rushed or schedules, its an ongoing process till the end-product is churned out. If the performance issues can be traced back to the design stage, then this is a big problem for both the client and manufacturer as a lot of time and money have been pumped into the project which increases the overall cost.
To counter such problems, it recommended creating a prototype mold that will take care of all these issues. You can also utilize 3D designer tech to provide plenty of insights on how to rectify such kinds of problems and make your product more functional.
The source of production issues
The core issues that create all these problems are outsourcing when your project is being worked on by many different firms and workshops; a lot of information will get passed around and some may get lost leading to mix-ups when it comes to transitioning from one company to another.
Manufacturers always work with the specs they are given, but the truth of the matter is most firms can produce the same product without these specifications. They will use the CAD files to produce your desired part or components based on their designs.
If the end-product is a failure, who will be blamed for that. As a client you should always outsource, you’re your product development to one company, this will reduce the miscommunication between different firms leading to project failure.
Dealing with performance issues
Given the way manufacturing business is headed, producers need to stay ahead of the curve by warding off competition from other firms. Most of the performance issues with most products date back to the design phase, thus it’s advisable to work with a company that casts our prototype mold using an efficient and effective method.
There will be no transition issues, and you will get the advantage of having professionals who are on-site working on your product.