Tool manufacturing is a complex and multifaceted process that begins with the registration of a request from a potential customer to the fabrication of the appropriate technological equipment. The more precise the information provided (drawing, technical specification, mathematical model), the faster professionals will be able to prepare an offer showing the cost and production time, as well as any order volume execution specifications. In some circumstances, rapid tooling options may be available with different options: materials. density in a form, etc.
Using CAD programs, the technical department’s specialists develop molds and punches according to the customer’s specifications. Drawings and specifications are developed based on the 3D model of the product and the tooling. In parallel, the cold forming and plastic foundry technologists evaluate the product for manufacturability and make recommendations to the designer for tool development.
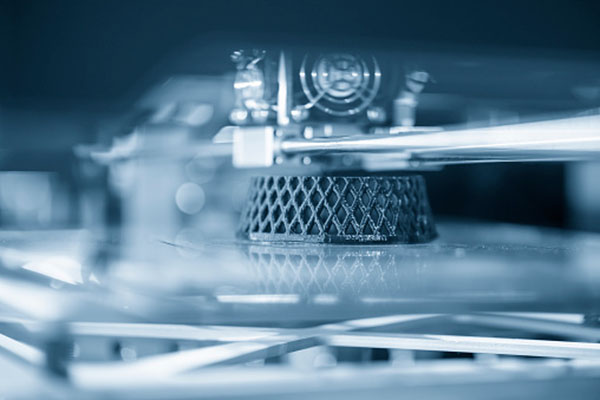
3d printing machines*
3d printing machines is from unsplash.com
After the design documents are approved, the project is passed on to the technologists, who work out the rapid tooling manufacturing technology and specify the workflow, material plans for the blanks, the need for electrodes, and so on.
If the customer is satisfied with the proposed terms, a contract for the design and manufacture of equipment (or production based on the customer’s design papers) is signed. Following the signing of the contract and receipt of the advance payment, the designers begin to create a project, which is subject to mandatory cooperation with the customer. If necessary, revisions and adjustments are made, and the specifics are worked out, then the project is taken to the foundry.
The technological process of producing the rapid tooling, as well as the technical programs of machining, are decided during the technological research, and second-order tools (special tools, devices, electrodes) are produced. Following that, the design and technical documentation are transmitted to the rapid tooling shop.
The following step is a whole cycle of manufacturing the technological equipment (molds, punches) in the factory’s tolling section. The workshop is divided into various production sites.
Molds and punches are manufactured at special facilities, which are outfitted with domestic and imported turning, drilling, grinding, and milling machines, as well as coordinate grinding machines.
Aside from these processes, you can choose to do the embossing of the mold surfaces of the tool elements as well as laser marking.
Auxiliary services are also provided in the workshop, such as repair, equipment maintenance, and tool sharpening.
Following production, the tools are tested with the support of the project’s lead technologist, measurement plans are created, and the final product’s compliance with the agreed-upon drawings is verified. If minor differences are discovered, the tools are refined until the final product is complete. Client representatives are invited to the testing, and if a business trip is not possible, the end items, along with the measurement cards, are sent to the customer for approval.
It is also possible to get a photo and video report. Following the review of the received samples, the tools (molds, punches) are accepted, and documentation is signed verifying the conformity of the manufactured tools with the designs and technical standards. Following that, the equipment is packed and placed at the customer’s method for transportation (or shipped by the transport company).