There are a lot of options when it comes to die casting metal available for making parts. If you landed here, you are probably looking for the best die casting products in the market. The task is not very difficult if you have a clear idea about the type of project you will work on. We are about to discuss some basics about die cast metal so you can discuss your options with your manufacturing company.
Types of Die Cast Metal Available
If we are discussing the most popular options of die cast metal, alloys are the ones who top the list. The most used ones are zinc, aluminum, and magnesium. There are other options that can be used as well, such as brass, copper, lead, and tin. These alloys are less-common and are often considered specialty materials for custom jobs in the die casting industry. Alloys are mixed elements, so metal die cast parts incorporate several of these materials. Since every alloy has a set of different properties, pros, and cons, the manufacturer needs to study the best options for the project at hand.
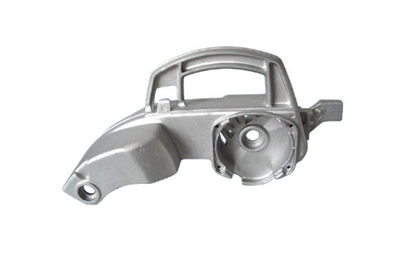
aluminum die casting power tool covers*
aluminum die casting power tool covers is from https://www.forcebeyond.com
Die Cast Metal for Vehicles
The manufacturing industry for vehicles parts favors die cast metal over other options all the time. They use a variety of materials since every vehicle is assembled using different specs. The most popular material on this industry it’s aluminum and aluminum-zinc alloys, even if they are some of the most expensive options out there. The main reason behind this is because aluminum and all derivatives of it have incredible corrosion-resistant properties that make them last more than other options. Aluminum also has one of the best strength/hardness/ weight ratios since it is very lightweight. This alloy is pretty easy to cast, and they are known for having some of the best electrical and thermal conductivity properties, which makes them an ideal option I other techs fields such as computing and energy management.
Die Cast Metal for Medical Equipment
Most of the metals used for medical equipment is closely related to the type of equipment that is being manufactured. The most popular options in this field are zinc, magnesium, and aluminum. Zinc castings are popular for items that are being customized aesthetically since the material offers a smooth surface to work on and can be plated or painted depending on the preferences of the patient. The material is also pretty lightweight, something that has to be considered if we are making appendixes for infants. Zinc also has a low melting point, something that favors a longer mold life. Last but not least, zinc has excellent corrosion resistance and enhanced thermal conductivity. This makes zinc quite durable, hard, and strong to offer dimensional stability.
The Traits of Die Cast Metal
As we stated previously, there are a ton of different applications suited for different metals. The metal that should be used in any die cast parts is always specific to the product being created, as well as the industry. There are a few generalities that have to be considered when we choose the best die cast metal. The first one is the ability to withstand high temperatures. Aluminum is the best one at this, but the manufacturer needs a cold chamber machine to treat it properly. Other materials such as zinc or magnesium can be handled with hot chamber machines which are more common in the industry.
If you need to create a lightweight component, magnesium is exceptionally light and the best material suited for these types of tasks. The only drawback is that magnesium has a limited presence in most manufacturing operations, and it’s often used for specialized jobs. The best of both worlds so far seems to be zinc alloys, since they are pretty easy to cast, and they retain their hardness as well as their strength for more extended periods than the other two main options. When it comes to corrosion, nickel is probably the best option, but this alloy is often used more by the food industry since it can hold food products without contaminating them.
Closing Thoughts
Choosing a die cast metal for a manufacturing project can be pretty tricky if you don’t have the right notion about what you need and the final purpose of it. The best way to go about this is to ask your manufacturer about the best options to handle your project. Die casting metals make almost any manufacturing project better because of the added value offered on durability alone. An in-depth study of the requirements of your project becomes a necessity for it to succeed. Try to keep in mind the brief knowledge you gathered here and create a strategy based on the affinity of the original project to an existing industry. You will be amazed at the things you learn with such a basic comparison.