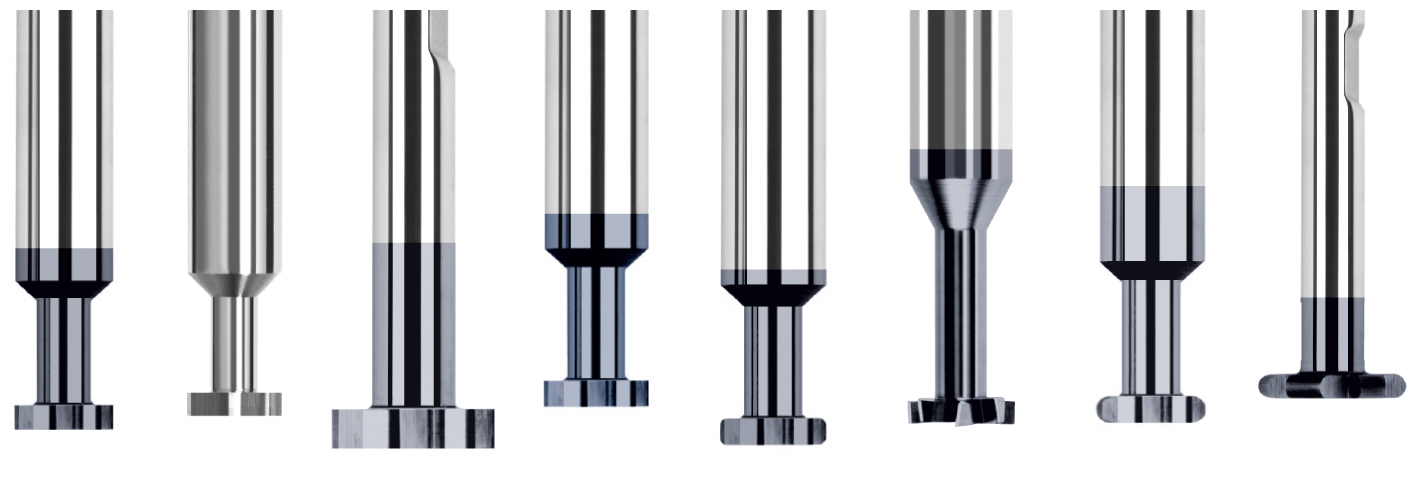
Keyseat Cutters, image from Harvey Tool
A Keyseat Cutter is essentially a tool that allows you to cut, mold and shape keyways and keys on a CNC machine. It also makes easier the work of handling keyseat tasks. The tool itself looks like a small rotary jaw and is mostly used when we have to fix a specific part on the shaft of certain types of machinery or on a sheave. When it comes to CNC machining services, it’s really helpful to understand just what we are dealing with to avoid confusion, so let’s clear up the basics concepts surrounding the use of keyseat cutters and the work that can be done with them.
For starters, a keyway is a slot used to align the parts of a shaft and keep them from moving as the shaft rotates. Keys are used inside the keyway to lock things in place and keep them from slipping and botching the work. When the key rest permanently on the keyway we refer to that component as a keyseat. The cutters specially customized to create these keyseats it’s what we call a keyseat cutter which it’s also referred as a Woodruff cutter to keep things simpler and avoid mixing terms that can sound too much alike in the workspace.
Working with a keyseat cutter requires prep time. The tool demands precision and proper engineering as well as the right calculation to achieve their potential. This is some of the advice gathered online when it comes to using these devices:
· Work the Right Geometry and Math
Measurements are on par with the ability to choose the right tools when it comes to prep work. It ranks even higher we dare to say. If we engage in a task with botched measurements such as wrong diameters and bad dialing speeds for the feeds, we will lose a great deal of time and materials. Even the pressure applied by the keyseat cutter has to be considered to avoid any deflection or breakages. The thickness of the neck on the cutter as well as its diameter will determine how successful the finished product is.
· Get a Solid Hold of the Radial Depth of the Cut
The radial Depth of Cut (RDOC) it’s what determines how far the tool will go to get the expected results on the task you working on. Many operators make the mistake of using RDOC’s at their maximum capabilities with no regard to the durability of the material that it’s being worked with. In the long run, this affects the quality of the parts being crafted and it can overwork the CNC machine unnecessarily.
· Get your Slot Sizes Right
There are way too many operators using keyseat cutters to craft slots that are larger in size than their cutters width. While there are no written rules about doing this “cheat” to save some money on the budget, the final results are less than desirable. It also delays the production cycle and overworks the CNC machine. If you genuinely need slots at specific sizes, you better budget for them to use the right tooling.
As you can see most of the advice is focused on handling the work with precision. Give the number of markets using parts manufactured using keyseat cutters, none of this information shouldn’t be taken lightly. A production run with failures will translate into bad business for future endeavors on the manufacturers’ end, and nobody wants that, right?