Many manufacturing processes are employed in manufacturing tools used in mold making. Some of these manufacturing processes include CNC machining, EDM operations, and 3D printing.
Today, mold makers are facing many challenges, but most of all, they are under enormous pressure to produce mold tooling more quickly than what they used to. Although they can use EDM manufacturing, many of them are exploring other manufacturing methods like CNC milling.
This article aims to find out the reasons why CNC milling is slowly replacing the EDM process of manufacturing.
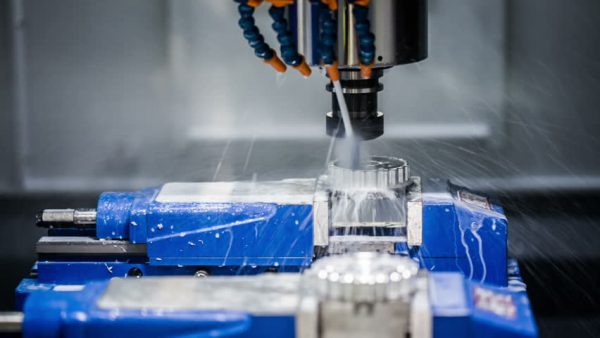
cnc milling machines*
cnc milling machines is from https://www.shutterstock.com
What is EDM?
In the EDM process, the electrical current is carried through the electrode that serves as a dielectric medium. This electrode is formed in the configuration of the part that will be taken away from the mold tooling. The spark, on the other hand, will remove the component to create the designed piece.
The persons responsible for developing the EDM or Electrical Discharge Machining process are the Lazarenko brothers in Russia during World War II.
The electrodes used in the EDM process are made mostly from carbon graphite. In recent times, copper alloys, brass, copper, and other materials are also used as electrodes. These electrodes are milled before using in the EDM machine.
The Advantages of Using EDM
There are some long-standing recognized advantages of adopting EDM machining, and that includes the following:
- It can be used in creating sharp inner corners. The top benefit of using EDM manufacturing is its ability to make sharp corners. In CNC milling, it will need tools of tiny diameters.
- It can create deep sections of the mold. EDM is preferred over CNC milling for its ability to cut into the deepest portion to create the right shape.
- EDM is best used in making complex shapes, and many have accepted this as conventional wisdom.
- Creating ribs in molding tools can be genuinely challenging because they are fragile. However, EDM manufacturing is commonly used to create them.
- It can function even unattended. Engineers prefer to use EDM sinker machines instead of CNC milling machine because they can leave it unattended.
In EDM, the surface finish can be specified. Most of the finishes in EDM manufacturing are consistent without swirl patterns or machining scallops.
How CNC Milling Has Taken Over EDM
If there is one place where you cannot use EDM, are in regions of HAZ or heat affected zones. These are weld areas where the temperature from the EDM operations cannot be tolerated and instead creates more problems than solutions. Because of the threshold stack-ups of holders and electrodes and not getting the exact dimensions of the spark, EDM is not applicable in parts that demand high precision.
EDM is a Slow Process
One of the most significant disadvantages of using EDM manufacturing is it’s slow. The first step in the process is to use CNC milling for the electrode. Most often, it needs more than one electrode in one area. Once the electrode is prepared, the EDM process will begin. The rate of material removal in EDM is slower than in CNC milling.
In short, not only is the EDM process is slow, but you also need CNC milling to prepare one or more electrodes. Aside from that, graphite electrodes are messy and dusty. It can lead to machine downtime if the machine has no built-in vacuum system to clean the graphite dust. This will not do for mold makers you want to produce molds quickly.
Even if CNC milling cannot do much on sharp corners, new software and technology can mitigate the advantages that EDM has.
In Milling the Deep Areas
The usual practice when a product design calls for difficult areas is to use EDM and electrodes. However, the emergence of 5-axis CNC mills in the mold making industry has transformed this. Now operators can rotate the machine’s tool axis for machining the deep areas without using EDM. The improvement of CAM software has simplified the capacities of many multi-axis machines.
In Rib Machining
It is difficult to mill ribs as it requires a tool with a large length/diameter ratio. These instruments are prone to breaking leading to another challenge, removing the chips in the rib. However, in spite of the difficulties, there is a faster way to do this other than EDM. Thanks to CAM systems, it now includes rib machining in the programming.
In Designs with Complex Geometries
Manufacturing products with complex geometry were once the forte of EDM, but now many of them are replaced with CNC milling. With the improvement of technology in all sections of machining, tools are now more rigid. CNC milling devices are also smoother and have built-in quick machining capability.
In Unattended Machining
By using simulation software in multi-axis machining, engineers can verify the programs if they are collision-free and can be operated unmanned. The algorithms are incorporated to switch cutting tools automatically.
Final Thoughts
The advancements in 5-axis machines, tool handling, and CAM programming software enabled CNC milling to replace many operations of the EDM manufacturing process. It has made faster production of molds and other related components required.