Anodizing is quite normal applied to the aluminum parts, it is much helpful for the corrosion and scratch resistance.
Aluminum part is easily oxidized when exposed to air, then the external surfaces will be corroded, and the part will be damaged over time. Besides, the anodizing coating is thinner than others processes coating, like painting, powder coating, it has the good heat dispersion.
Like this heatsink, our customer originally asked for powder coating, but he found the cooling effect is not so good, and the coating was cracked on some areas. We finally suggested to use anodizing process, the problem had been solved immediately.
But one thing, anodizing coating on the pressure die casting parts, it can not achieve perfect surface, the main issue is the coating does not distribute on the surface evenly. For the aluminum alloy, there are actually many components inside the material, like silicon,copper, iron, etc.
During the anodizing, silicon can cause grey color coating on the surface. Especially when the containing over 4.5%, the grey will be quite obvious, copper can cause red color and iron can cause black dot. Using the black anodizing on ADC-12 casting part as an example, some areas are dark black, some areas are dark grey, and some areas are slight red. But black is still the main color.
This is worldwide problem which can not be solved so far. The reason is that the free elements in the aluminum alloy material will distribute on the external surfaces randomly and irregularly.
So anodizing is always applied to the die casting parts which have no high quality requirement of the appearance. But for pure aluminum parts, anodizing coating can be made perfect since there is very little metal impurities mix inside the material, such as AL-6061, 6063,7075 etc.
Besides, the anodizing can be made as different colors, like black, natural, green, blue and so on.
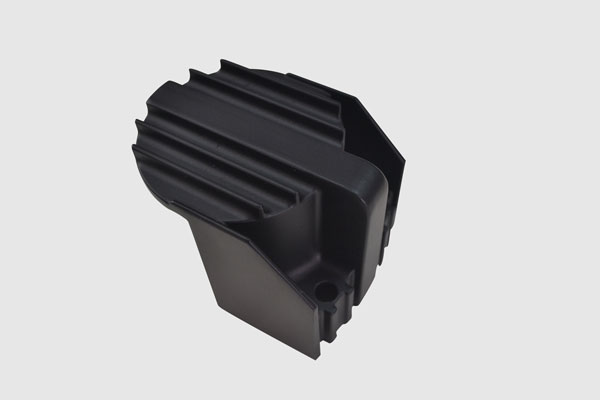