If you want to get your product to market as quickly as possible, rapid prototyping will be necessary to have the parts readily available for testing. In recent years, there have been several technological advancements in the manufacturing business. Among them are the numerous fast prototyping approaches that may be used to assist the design team throughout the product development phase of the project. Rapid prototyping is the term used to describe this process.
Because of fast Tooling, components may be produced rapidly to test and validate before being put into production tooling for mass production. A variety of names refers to the process of rapid Tooling. Prototype tooling, soft tooling, and prototype mold are all terms used to describe this process. For the time being, let’s stay with fast Tooling.
This essay will go deeper into the meaning of this term and examine its benefits and uses. Let us first define what quick Tooling is and how it differs from traditional Tooling.
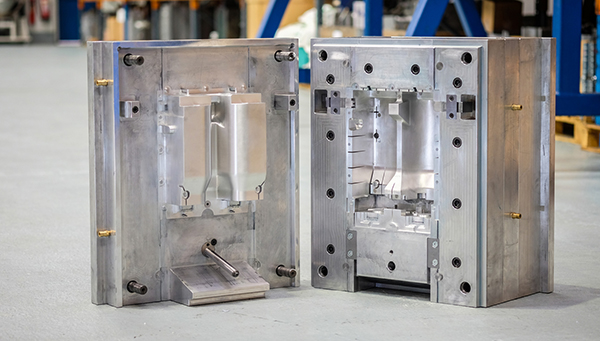
aluminium toolings
aluminium toolings is from rptechnologies.co.uk
Rapid Tooling is just getting started
In its most basic definition, Rapid Tooling is the process of making a prototype in a short period. It all started in the 1990s when engineers working with plastic injection molding attempted to develop ways to make molds in days or even hours rather than the months it took them to produce a machine mold.
Pieces produced by fast Tooling are an excellent solution for testing and evaluating a prototype and producing a few hundred parts before entering into total production. Rapid tooling procedures are used to create inserts for the components, such as the core, side actions, and cavities. It all relies on the fast Tooling that is being used; it can produce components via many cycles from the same mold.
There are many different quick tooling processes to select from, and each one has its own set of advantages. Because it varies based on the size, consistency, technology, precision, and materials you will employ, there are several aspects to consider to reap the most significant benefit from these advantages outlined above. If you are contemplating quick Tooling to create your prototype, you should also consider the following constraints.
The mold should be highly durable
The mould must be long-lasting to withstand the stresses of the injection molding process. Molds should be able to resist the injections since the molding machinery clamped hot materials into the mold at a rate of pounds per inch.
The mold should have a smooth surface
Aside from being robust, it should also be smooth to allow for clean plastic injection. Having this quality is essential since it is required for every expulsion. Some techniques in fast Tooling add materials layer by layer, resulting in a non-smooth surface. If such is the case, the prototype will require extra polishing before being used for prototyping.
The Advantages of Rapid Tooling
Here are some more advantages of fast Tooling. It gives a chance for experimentation and creativity. The elimination of the need for conventional Tooling opens the door to a whole new set of options for improvement since fast Tooling eliminates the need for traditional Tooling.